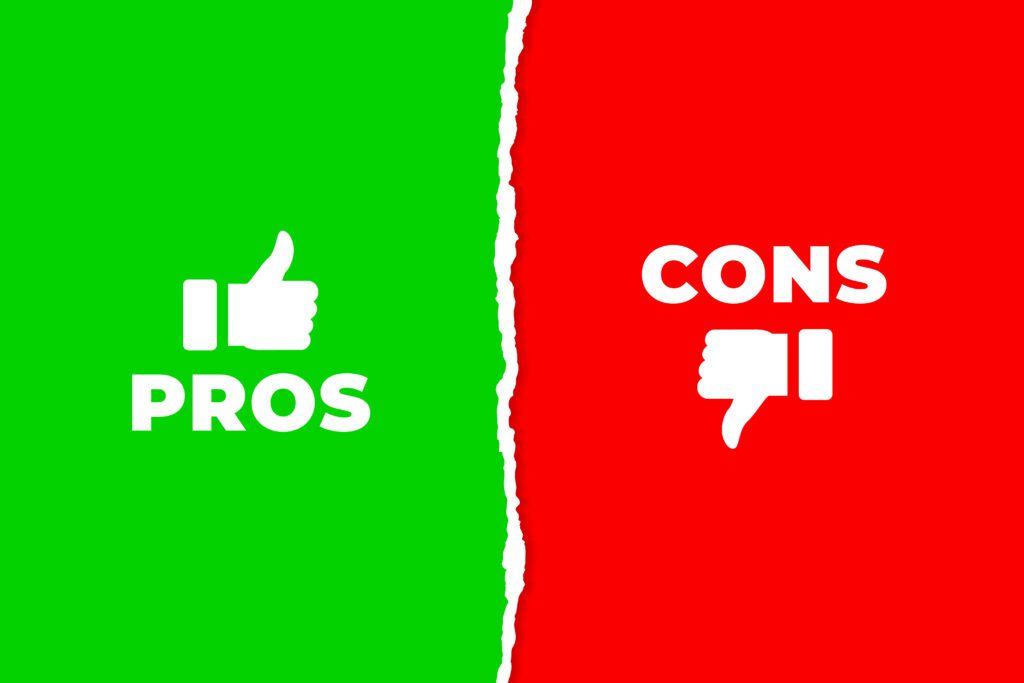
Pros and Cons of Foam Insulation – Polyiso vs XPS vs EPS
Rigid foam insulation plays a critical role in building envelope performance, balancing thermal resistance, moisture management, and structural durability. Among the most widely used materials in this category are Extruded Polystyrene (XPS), Expanded Polystyrene (EPS), and Polyisocyanurate (Polyiso)—each engineered through distinct manufacturing processes that yield markedly different physical and thermal properties. This article provides a detailed comparative analysis of these materials, synthesizing empirical data and industry standards to guide architects, contractors, and energy consultants in selecting the optimal insulation for climate-specific and application-driven scenarios. From long-term thermal resistance (LTTR) and vapor permeability to fire performance and embodied carbon, this evaluation moves beyond simple R-value comparisons to inform high-performance, sustainable design.
For professionals seeking to maximize both environmental and economic efficiency, Green Insulation offers a practical, planet-friendly solution: reclaimed XPS, EPS, and Polyiso foam boards. Sourced from commercial deconstruction and surplus inventory, our reclaimed insulation products not only divert high-performance materials from landfills but also provide significant cost savings without compromising on quality. Whether you’re designing a net-zero retrofit or aiming to meet stringent green building certifications, Green Insulation empowers you to build smarter—reducing your project’s carbon footprint while preserving its thermal integrity. Visit GreenInsulationGroup.com to explore our current inventory and make your next build a sustainable one.
Here is a concise yet comprehensive comparison of the physical and thermal performance characteristics of three widely used rigid foam insulation materials: Extruded Polystyrene (XPS), Expanded Polystyrene (EPS), and Polyisocyanurate (Polyiso).
Table 1: Summary Comparison of Key Properties (XPS, EPS, Polyiso)
Property | Extruded Polystyrene (XPS) | Expanded Polystyrene (EPS) | Polyisocyanurate (Polyiso) |
Typical R-value/inch @75F | R-5.0 | R-3.8 – R-4.5 (density dependent) | R-5.6 – R-7.0 (facer/product dependent, often ~R-6.5) |
Typical LTTR/inch | R-5.0 | N/A (Stable R-value) | R-5.6 – R-6.0+ (thickness/product dependent) |
Cold Temp R-value Trend | Stable / Slight Increase | Stable | Decreases below ~50°F |
Water Absorption (% vol) | Very Low (0.1 – 0.3%) | Low to Moderate (2.0 – 4.0%, density dependent) | Low to Moderate (1.0 – 3.0%, facer/source dependent) |
Vapor Permeability (1″) | Low (~1.1 – 1.5 perm) | Moderate (~2.0 – 5.0 perm, density dependent) | Very Low (<0.05 perm, Foil-Faced) to Moderate (<1.0 – <5.0 perm, Glass-Faced) |
Compressive Strength (psi) | High (15 – 100 psi) | Variable (10 – 60 psi, density dependent) | Standard (16 – 25 psi); HD Cover Boards available |
Fire Behavior | Thermoplastic (Melts/Drips) | Thermoplastic (Melts/Drips) | Thermoset (Chars) |
Relative Cost/R-value | Medium | Low | High |
Extruded Polystyrene (XPS) is well-suited for below-grade applications due to its excellent water resistance and high compressive strength. Expanded Polystyrene (EPS), offering variable properties based on density, is a versatile and cost-effective option for walls and some roof applications. Polyisocyanurate (Polyiso) provides the highest R-value per inch, making it ideal for roofs and walls where maximum thermal resistance in a thinner profile is needed, although its performance can be affected in very cold temperatures.
Foam Type | Below Grade Use | Roof Use | Wall Use |
XPS | Best Suited: Excellent water resistance & high compressive strength. | Good option, requires more thickness than Polyiso for same R-value. | Good general wall insulation, good moisture resistance. |
EPS | Usable (density dependent), less water resistant than XPS. | Good option (density dependent), requires more thickness than Polyiso. | Versatile/Cost-Effective: Suitable for various wall systems, performance depends on density. |
Polyiso | Less Ideal: R-value decreases in cold temps, standard compressive strength lower than XPS. | Best Suited: Highest R-value/inch, chars in fire, good with cover boards. | Best Suited: High R-value where space is limited. Foil-faced acts as vapor barrier. Consider cold temp R-value. |
Detailed Properties of Foam Board Insulation Types
XPS, EPS, and Polyiso represent three distinct types of rigid foam insulation, each manufactured through different processes leading to unique microstructures and performance characteristics. XPS is produced via an extrusion process, resulting in a homogeneous closed-cell structure with a smooth skin. EPS is created by expanding polystyrene beads within a mold, forming a closed-cell structure but with interstitial voids between the fused beads. Polyiso is a thermosetting plastic foam, typically manufactured in a lamination process between facers, resulting in a closed-cell structure formed through chemical reaction. Understanding the inherent differences in their properties is crucial for appropriate material selection and effective building envelope design.
1.1 Thermal Performance
Thermal performance is a primary function of insulation, typically quantified by R-value, which measures resistance to heat flow; a higher R-value indicates better insulating power. While materials with the same R-value offer equivalent insulation if installed and air-sealed correctly, the R-value itself can vary based on material type, density, temperature, and aging.
- R-value per Inch:
- Polyiso: Generally provides the highest thermal resistance per unit thickness among the three, with typical R-values ranging from 5.6 to 7.0 per inch (hr⋅ft2⋅°F/Btu⋅in), often cited around R-6.5 for faced products. This allows designers to achieve target R-values with less insulation thickness compared to XPS or EPS.
- XPS: Offers a high R-value, typically R-5.0 per inch. Specific products like DuPont™ Styrofoam™ cite R-5.0 per inch long-term R-value, while Owens Corning FOAMULAR® 250 (1-inch) lists R-5.0 at 75°F mean temperature.
- EPS: Provides R-values ranging from approximately R-3.8 to R-4.5 per inch, depending primarily on density. Achieving the same total R-value requires greater thickness compared to XPS or Polyiso.
- Long-Term Thermal Resistance (LTTR):
Foam insulations manufactured with blowing agents other than air can experience a phenomenon called thermal drift, where the initial high R-value decreases over time as the blowing agent slowly diffuses out and air diffuses in. LTTR is a standardized method (e.g., CAN/ULC S770-03, ASTM C1289) intended to provide a scientifically supported, 15-year time-weighted average R-value to account for this aging effect.
- Polyiso: LTTR values are widely published for roofing products, typically ranging from R-5.6 to R-6.0+ per inch, increasing slightly with thickness. Impermeable facers are crucial for maintaining the LTTR by slowing gas diffusion.
- XPS: Manufacturers also provide LTTR values; for example, Owens Corning FOAMULAR® 250 (1-inch) lists an LTTR of R-5.0 per inch. XPS is generally recognized for good R-value retention over time, even under adverse conditions.
- EPS: Since EPS primarily uses air as its insulating gas (pentane is used as the blowing agent during manufacturing but dissipates quickly), it is not subject to the same long-term thermal drift and its R-value is considered stable over time.
- Temperature Dependency of R-value:
Standard R-value tests are conducted at a mean temperature of 75°F (23.9°C). However, insulation performance can change significantly at different operating temperatures encountered in building envelopes.
- Polyiso: The thermal performance of polyisocyanurate insulation is notably sensitive to temperature. Research by the National Roofing Contractors Association (NRCA) and Building Science Corporation (BSC) has shown that polyiso’s R-value tends to decrease as the mean temperature deviates significantly from the standard 75°F test condition, particularly at colder temperatures typical of winter conditions in many climates. For instance, R-values measured at 25°F (-3.9°C) can be substantially lower than those measured at 75°F.
- NRCA Recommendation: Recognizing the impact of aging and temperature, the NRCA advises designers against relying solely on published LTTR values for polyiso. Instead, they recommend using a lower in-service R-value for design calculations, suggesting R-5.0 per inch for cold climates or R-5.6 per inch for warm climates, or a general R-5.0 per inch, to better reflect expected performance under actual operating conditions.
- XPS: In contrast to polyiso, XPS generally maintains its R-value better at lower temperatures. Test data for products like FOAMULAR® 250 show that the R-value actually increases slightly as the mean temperature decreases (e.g., R-5.0 at 75°F, R-5.4 at 40°F, R-5.6 at 25°F).
- EPS: The R-value of EPS is considered relatively stable and consistent across a wide range of temperatures.
- Performance Implications: The difference in temperature dependency, particularly the reduction in polyiso’s R-value in cold conditions, stems from the physics of the blowing agents used within the foam cells and how their thermal conductivity changes with temperature. Standardized LTTR testing, while valuable for comparing aged R-values under specific conditions, does not fully capture this temperature-dependent behavior. This discrepancy between standardized test results and potential in-service performance under cold conditions has led building science practitioners and organizations like NRCA to advocate for more conservative R-values in design calculations for polyiso, especially in heating-dominated climates, to ensure the building envelope achieves the intended thermal resistance during critical cold periods.
1.2 Moisture Resistance
Moisture performance encompasses both resistance to liquid water absorption and the ability to manage water vapor diffusion. Both aspects are critical for maintaining thermal performance and ensuring the durability of the building envelope.
- Water Absorption:
- XPS: Possesses a homogeneous closed-cell structure that results in very low water absorption, typically reported between 0.1% and 0.3% by volume according to ASTM C272 tests. This high resistance to moisture makes XPS particularly well-suited for applications where it may be exposed to damp conditions or direct water contact, such as below-grade walls, foundations, and under slabs. Some sources claim XPS absorbs significantly less water than polyiso and is up to 13 times more resistant than EPS.
- Polyiso: Generally more susceptible to moisture absorption than XPS. Reported values vary, with some sources indicating up to 3% by weight, while product data tables might show 1.0% by volume for faced products. Absorption can negatively impact its R-value. Its suitability for high-moisture environments is limited compared to XPS.
- EPS: Water absorption varies with density, typically ranging from 2.0% to 4.0% by volume. While its fused-bead structure is described as essentially impermeable with zero capillaries, moisture can be absorbed through the fine interstitial channels between beads when immersed. Despite higher absorption than XPS, certain types of EPS are approved for below-grade use.
- Water Vapor Permeability:
Permeability describes how easily water vapor can pass through a material, measured in perms (perm-inch for material property). This property influences an assembly’s ability to dry out if moisture enters.
- XPS: Generally has low water vapor permeability, typically less than 1.5 perms for 1-inch thickness (often around 1.1 perms). This classifies it as a Class II or III vapor retarder depending on thickness (permeance decreases as thickness increases). Its low permeability restricts drying through the insulation layer.
- Polyiso: Permeability is highly dependent on the type of facer used. Foil-faced polyiso is a Class I vapor barrier with very low permeance (e.g., 0.03 perms). Glass-fiber or other non-metallic facers result in higher permeability, often classified as Class II or III vapor retarders (e.g., <1.0 to <5.0 perms depending on source and specific facer). Unfaced polyiso would be more permeable. The low permeability of foil-faced products necessitates careful design to avoid trapping moisture within the assembly.
- EPS: Generally considered vapor semi-permeable, allowing for greater drying potential compared to XPS or foil-faced polyiso. Typical perm ratings for 1-inch thickness are around 2.0 to 5.0 perms, decreasing with increased density or thickness.
- Design Implications: A fundamental challenge in material selection arises from the interplay between water absorption resistance and vapor permeability. Materials like XPS, which excel at resisting bulk water absorption, often exhibit low vapor permeability. This characteristic, while beneficial in preventing wetting, can impede the drying of incidental moisture that might enter the assembly through other pathways (e.g., air leaks, construction moisture). Conversely, materials like EPS offer higher vapor permeability, facilitating drying, but generally have higher water absorption rates. Polyiso provides flexibility, as its permeability is largely controlled by the choice of facer. This inherent trade-off underscores the importance of designing the building envelope as a system, carefully considering the vapor profile, potential wetting sources, and required drying mechanisms based on the chosen insulation type, its placement, the climate, and other assembly components.
1.3 Mechanical Properties
- Compressive Strength:
This property indicates the insulation’s ability to resist deformation under load, crucial for applications involving direct pressure or structural support.
- XPS: Is known for its durability and is available in a wide range of compressive strengths, typically from 15 psi up to 100 psi (ASTM D1621 minimums). This makes it suitable for demanding applications like below-grade walls, under slabs, plaza decks, and situations involving heavy construction loads.
- EPS: Compressive strength is directly related to its density, typically ranging from 10 psi to 60 psi (ASTM C578 types). While customizable, standard EPS types generally have lower compressive strength than the higher grades of XPS. EPS geofoam is specifically engineered for geotechnical applications requiring controlled compressive resistance.
- Polyiso: Standard roofing and wall insulation products typically offer minimum compressive strengths of 16 psi or 20-25 psi. While adequate for many wall and roof applications, this is generally lower than the upper range available with XPS. High-density (HD) polyiso cover boards are available specifically for roofing applications requiring enhanced strength and impact resistance.
- Dimensional Stability:
Rigid foam insulations must maintain their shape and size under varying temperature and humidity conditions. Standards like ASTM D2126 specify maximum allowable linear change (typically 2.0%). XPS is noted for good dimensional stability. Concerns about dimensional stability and potential facer delamination contribute to NRCA’s recommendation to limit individual polyiso board thickness to 2.5 inches in multi-layer roofing applications.
1.4 Fire Performance & Safety
All foam plastic insulations are combustible materials and require specific fire safety considerations in building design and construction.
- Polyiso: Is a therm
Rigid foam insulation plays a critical role in building envelope performance, balancing thermal resistance, moisture management, and structural durability. Among the most widely used materials in this category are Extruded Polystyrene (XPS), Expanded Polystyrene (EPS), and Polyisocyanurate (Polyiso)—each engineered through distinct manufacturing processes that yield markedly different physical and thermal properties. This article provides a detailed comparative analysis of these materials, synthesizing empirical data and industry standards to guide architects, contractors, and energy consultants in selecting the optimal insulation for climate-specific and application-driven scenarios. From long-term thermal resistance (LTTR) and vapor permeability to fire performance and embodied carbon, this evaluation moves beyond simple R-value comparisons to inform high-performance, sustainable design.
Call to Action – Green Insulation
For professionals seeking to maximize both environmental and economic efficiency, Green Insulation offers a practical, planet-friendly solution: reclaimed XPS, EPS, and Polyiso foam boards. Sourced from commercial deconstruction and surplus inventory, our reclaimed insulation products not only divert high-performance materials from landfills but also provide significant cost savings without compromising on quality. Whether you’re designing a net-zero retrofit or aiming to meet stringent green building certifications, Green Insulation empowers you to build smarter—reducing your project’s carbon footprint while preserving its thermal integrity. Visit GreenInsulationGroup.com to explore our current inventory and make your next build a sustainable one.oset material, meaning it tends to char and form a protective layer when exposed to flame, rather than melting and dripping. This characteristic generally gives it superior fire resistance compared to thermoplastic foams like EPS and XPS. Polyiso is often included in fire-tested wall assemblies meeting standards like NFPA 285.
- XPS & EPS: Are thermoplastic materials that will soften, melt, and drip when exposed to sufficient heat or flame. This behavior can potentially contribute to fire spread. They generally require specific assembly designs or additional protective measures to meet stringent fire tests like NFPA 285, particularly in commercial steel stud walls.
- General Requirements: Regardless of type, foam plastic insulation must typically be separated from interior occupied spaces by a thermal barrier, such as 1/2-inch gypsum board, or be part of a tested and approved assembly that does not require one. Products must meet flame spread and smoke developed index requirements per tests like ASTM E84.
1.5 Environmental Considerations
The environmental impact of insulation materials involves factors from manufacturing (blowing agents, embodied energy) to end-of-life (recyclability).
- Blowing Agents: Historically, some foam insulations used blowing agents with high ozone depletion potential (ODP) or global warming potential (GWP). Current formulations for XPS and Polyiso utilize blowing agents with zero ODP and significantly reduced GWP compared to previous generations. EPS manufacturing uses pentane, a blowing agent with low GWP and zero ODP, and the final product consists largely of trapped air.
- Recycled Content: Manufacturers increasingly incorporate recycled content into foam insulation products. Both pre-consumer and post-consumer recycled content can be found in EPS, XPS, and Polyiso, though percentages vary by manufacturer and product line.
- Recyclability: All three foam types can potentially be recycled, often through reuse or reprocessing, although the availability of recycling programs and infrastructure varies geographically.
- Embodied Carbon/Energy & Life Cycle Assessment (LCA): While the primary environmental benefit of insulation lies in reducing operational energy consumption over a building’s life, there is growing attention on the environmental impacts associated with manufacturing and transporting the insulation itself – its embodied energy and carbon. Environmental Product Declarations (EPDs), based on LCA methodologies, provide standardized data on these impacts. However, studies have noted potential inconsistencies between EPDs from different sources, even for similar materials, highlighting the need for careful selection and interpretation. The energy savings achieved over the insulation’s service life are typically estimated to far exceed the initial embodied energy. Nonetheless, the increasing focus on whole-life carbon necessitates a more holistic assessment beyond just operational R-value and cost. This trend is driving research into alternative, lower-impact materials like bio-based foams and emphasizes the need for reliable, comparable EPD data to inform sustainable material choices.
1.6 Cost Considerations
Cost is a significant factor in material selection. The relative costs per unit of R-value generally follow a pattern:
- EPS: Typically offers the lowest cost per R-value per inch, estimated around $0.25-$0.30 per square foot for a 1-inch panel.
- XPS: Occupies a mid-range position, estimated around $0.42 per square foot for a 1-inch panel.
- Polyiso: Generally has the highest initial material cost per R-value per inch, estimated around $0.70 per square foot for a 1-inch panel.
However, simple material cost per R-value does not capture the full economic picture. Polyiso’s higher R-value per inch might lead to savings in fastener lengths or allow thinner overall assemblies. XPS’s specific properties like high strength or moisture resistance might justify its cost in certain demanding applications. The overall cost-effectiveness must consider the total installed cost, including labor, detailing complexity, and potential long-term performance benefits or risks associated with each material in the specific application context.
Ready to Build Smarter?
Explore our full inventory of reclaimed XPS, EPS, and Polyiso insulation boards—available at a fraction of the cost and environmental impact of new materials. Whether you’re optimizing for performance, sustainability, or budget, Green Insulation offers the expertise and supply chain transparency to support your next high-efficiency build. Contact us today to request a quote, check availability, or learn more about how reclaimed materials can elevate your project’s performance and sustainability profile.