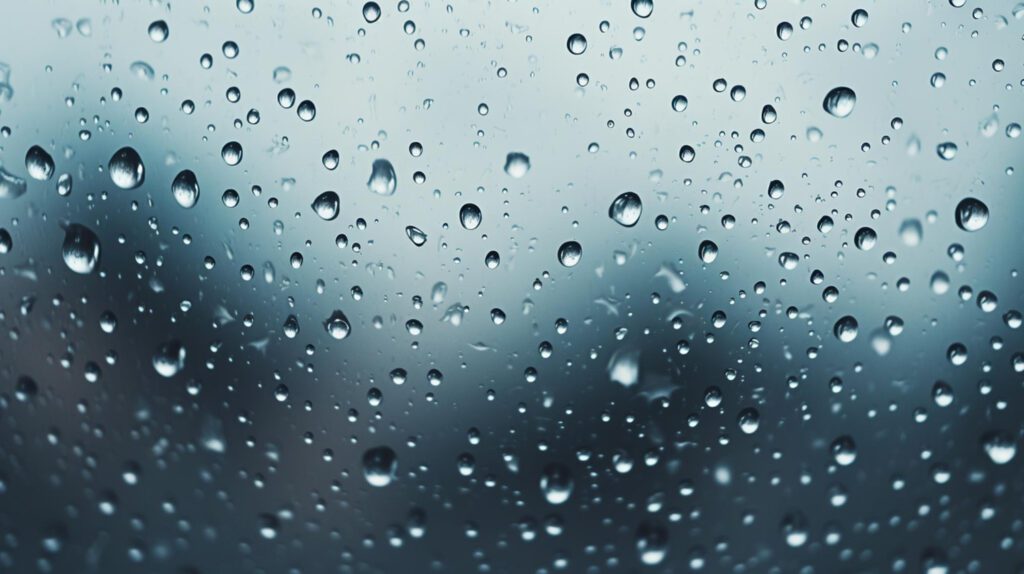
How XPS EPS and Polyiso Insulation Perform Against Moisture
When choosing insulation, particularly reclaimed foam panels, one of the most critical performance factors to consider is moisture resistance. Whether you’re working on a foundation retrofit or insulating a roof deck, understanding how insulation responds to water exposure can make the difference between long-term energy efficiency and costly building envelope failures.
Moisture resistance determines how well insulation retains its thermal performance under wet conditions. Water, when absorbed into insulation, displaces air within the material’s structure. This disrupts the insulation’s ability to resist heat flow, leading to reduced R-value and, in some cases, structural degradation. Moisture-laden insulation can also foster mold growth, posing health risks and contributing to indoor air quality issues. These are not theoretical concerns—in field applications, improperly installed or compromised insulation is often a hidden driver of performance shortfalls and building decay.
Trust Green Insulation for Clean, Moisture-Resistant Foam Boards
Our reclaimed XPS, EPS, and polyiso panels are carefully sourced from commercial roofing systems, expertly inspected, and performance-graded to ensure they meet the highest standards. Skip the guesswork—get insulation that performs like new at a fraction of the cost.
How XPS, EPS, and Polyiso Compare in Moisture Performance
Among rigid foam insulation types, extruded polystyrene (XPS), expanded polystyrene (EPS), and polyisocyanurate (polyiso) each offer distinct moisture profiles. XPS, due to its dense closed-cell structure, exhibits the lowest water absorption and is often favored in below-grade applications like basement walls or slab-on-grade floors. EPS, while still a closed-cell material, is more permeable to moisture and has higher absorption rates, especially if its surface has been damaged or lacks protective facings. However, its drying potential is better, making it suitable in assemblies that can tolerate intermittent moisture exposure.
Polyiso, in contrast, tends to be highly resistant to moisture penetration when its foil or coated facers remain intact. But once facings are compromised, polyiso’s moisture behavior becomes more variable, as its core can absorb water and lose thermal performance faster than either XPS or EPS. This makes inspection and installation technique especially critical for reclaimed polyiso boards.
What Makes Reclaimed Foam Different?
The moisture performance of reclaimed foam panels is influenced not just by material type but by the condition and history of the boards. While new foam comes with standardized test data, reclaimed insulation has already been through one life cycle of use—often on rooftops or walls where exposure to rain, condensation, or mechanical damage is possible. The result is that some reclaimed panels may exhibit diminished water resistance if they have been previously saturated, improperly stored, or physically compromised during removal.
However, not all reclaimed insulation is created equal. Panels salvaged from commercial roofing systems, for example, are often well-protected by membranes and tend to be in excellent condition. Reputable suppliers sort, clean, and grade panels before resale, screening out materials with signs of delamination or moisture damage. In many cases, reclaimed panels that were never exposed to water in their prior use can perform as well as new insulation.
Installation Practices to Enhance Moisture Protection
Even the most water-resistant insulation can fail if installed incorrectly. For reclaimed foam boards, the risk of moisture intrusion can be minimized through proper detailing and system design. Joints between panels should be tightly fitted and sealed using compatible tapes or spray foams to prevent bulk water intrusion and air leakage. In below-grade or foundation applications, it’s critical to provide a drainage layer between the insulation and soil, and to protect the panels with a waterproofing membrane or dimple mat.
Roof assemblies using reclaimed foam must account for both vapor diffusion and mechanical water entry. This often means including a vapor retarder on the warm side of the assembly, using cover boards, and ensuring continuous exterior layers without thermal bridging. In all cases, the integrity of the reclaimed foam is only as good as the assembly it’s installed in—careful integration with flashing, structural elements, and sealants is essential.
Meeting Standards and Expectations Without Formal Certification
Because reclaimed insulation has already been used, it does not carry the same manufacturer-backed certifications as virgin material. However, many performance characteristics—such as compressive strength and moisture resistance—can still be evaluated using industry standards like ASTM C578 for EPS and XPS, or ASTM C1289 for polyiso. Some suppliers conduct in-house testing or partner with third-party labs to verify that reclaimed boards meet baseline performance thresholds.
Although reclaimed foam cannot be formally “certified” in the same way as new product lines, informed selection and proper testing can ensure that performance remains consistent with application needs. For critical applications, it may be worth spot-testing random samples for density, water absorption, or thermal resistance.
Long-Term Efficiency Starts with Moisture Control
Insulation’s role in energy efficiency only holds if its thermal performance remains stable over time. When foam insulation becomes saturated, its R-value can plummet—sometimes by more than 50 percent depending on the material and conditions. This means that a poorly detailed wall or roof assembly with otherwise high-quality insulation can still underperform simply due to moisture ingress.
Particularly in cold climates or coastal zones, moisture intrusion can occur through vapor diffusion, wind-driven rain, or capillary action. By using reclaimed foam that’s been properly evaluated and combining it with a robust installation strategy, builders and designers can reduce embodied carbon without compromising performance. Reclaimed materials also align well with utility-backed energy efficiency programs and green building certifications, further extending their value.
Common Myths About Moisture and Reclaimed Insulation
A persistent myth is that reclaimed foam boards are inherently damaged or moisture-logged, but this generalization ignores the rigorous sorting and testing that many suppliers apply. Another common misconception is that reclaimed boards cannot be used in wet conditions such as foundation walls or roofing—yet both applications are not only feasible, but often highly effective when the right foam type and installation details are employed. While it is true that damage or prior water exposure can degrade foam, properly sourced panels—especially XPS and foil-faced polyiso—retain excellent moisture resistance.
Moisture resistance is a key determinant of insulation success, and with the right knowledge and sourcing practices, reclaimed foam panels can meet or exceed expectations. Understanding how different foam types behave under moisture stress—and how to install them correctly—empowers builders to choose sustainable, high-performance solutions. When in doubt, partner with a supplier who can provide documentation, guidance, and material traceability. With care and insight, reclaimed insulation can contribute to durable, dry, and energy-efficient buildings for decades to come.
Ready to Build Smarter with Reclaimed Insulation?
Contact Green Insulation today to find high-performance XPS, EPS, and polyiso foam boards that meet your project’s needs. Our team is here to help you choose sustainable, cost-effective materials without compromising on quality.