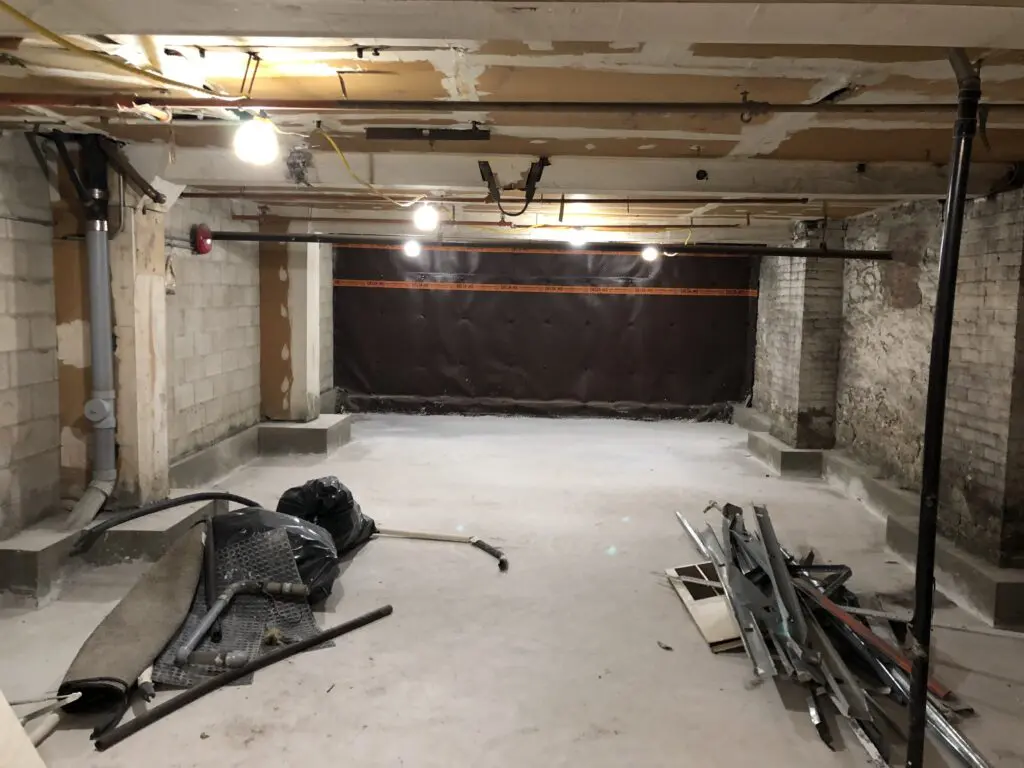
DIY Guide: Installing Reclaimed Rigid Foam Panels for Basement Insulation
Transform Your Basement with Cost-Effective Reclaimed Insulation
Imagine a basement that’s no longer a chilly, damp storage area, but a warm, dry, and comfortable extension of your living space. Picture lower energy bills and the satisfaction of having made a smart, eco-friendly upgrade to your home. This is all achievable with the right insulation, and even better, you can do it yourself! This guide will walk you through installing reclaimed rigid foam insulation in your basement, a project that’s both budget-friendly and surprisingly manageable.
Reclaimed rigid foam, such as XPS (Extruded Polystyrene) or EPS (Expanded Polystyrene), is insulation that has been salvaged from previous applications, like commercial roofing projects, and is now ready for a second life in your home. It’s a fantastic choice for basements because it offers excellent R-value (its ability to resist heat flow), good moisture resistance, and significant cost savings compared to new materials. Plus, by choosing reclaimed, you’re making a sustainable choice that reduces waste. At Green Insulation, we specialize in providing quality, inspected reclaimed XPS and EPS panels perfect for your DIY basement project.
So, why bother insulating your basement? A well-insulated basement is key to overall home energy efficiency. It helps control moisture, which can prevent mold and mildew growth, and it transforms an often-underutilized area into potentially valuable living space. With this guide, you’ll see how DIY reclaimed insulation can make a big difference. We’ll cover everything from planning and preparation to the step-by-step installation of basement insulation XPS or EPS panels.
For sustainable and cost-effective building solutions, consider Green Insulation. As a leading distributor of quality reclaimed XPS and EPS rigid foam panels, we are proudly based in Worcester, Massachusetts, and serve the entire New England region. Contact us to discuss your needs and see how reclaimed insulation can benefit your next project.
Before You Begin: Planning & Preparation for Your DIY Reclaimed Insulation Project
Proper planning is the cornerstone of any successful DIY endeavor. Before you even think about cutting your first foam panel, let’s cover some essential groundwork.
First and foremost, safety is paramount. Always wear appropriate Personal Protective Equipment (PPE), including gloves to protect your hands, safety glasses to shield your eyes from debris, a dust mask or respirator (especially when cutting foam), and long sleeves to cover your skin. Ensure your work area has proper ventilation, particularly if you’re using adhesives or cutting a lot of foam. Be mindful of electrical safety; identify any outlets, wiring, or fixtures in your work area and take precautions when working around them.
Next, take some time to understand your basement walls and any local building codes. Are your walls made of concrete or block? This might influence your attachment method. More importantly, thoroughly inspect your walls for any existing moisture issues. Look for signs like efflorescence (a white, powdery substance), damp spots, active leaks, or cracks. These must be addressed before you install any insulation, as trapping moisture can lead to bigger problems down the line. It’s also wise to briefly check with your local building department regarding insulation requirements for basements in your area. They may have specific R-value targets, or rules about vapor barriers and fire barriers.
Now, let’s talk about choosing your reclaimed rigid foam. For basements, both XPS and EPS are good options. XPS (often pink or blue) generally offers a slightly higher R-value per inch and greater moisture resistance, making it a popular choice for below-grade applications. EPS (usually white) can be more cost-effective and is still a very capable insulator. When you source your used foam board from a reputable supplier like Green Insulation, you can be confident you’re getting quality, inspected panels. You’ll also need to determine the appropriate thickness and R-value for your climate and basement conditions.
To make sure your project goes smoothly, gather all your tools and materials beforehand. Here’s a general checklist:
- Reclaimed rigid foam panels (XPS or EPS) from Green Insulation
- Measuring tape
- A sharp utility knife with plenty of extra blades (or a specialized foam knife/saw for thicker boards)
- A straight edge or T-square for guiding your cuts
- A caulking gun
- Foam board adhesive specifically designed for XPS/EPS compatibility
- Construction adhesive (if you plan on building a wood frame)
- Seam tape (such as house wrap tape or specialized foam board tape)
- Expanding foam sealant for filling gaps
- Optionally, you might need lumber (like 2x2s or 2x4s) and fasteners if you’re building a frame, a vapor barrier if required by code or desired for your situation, and a fire-rated covering like drywall (which is often a code requirement).
Finally, prepare the basement walls. Clean them thoroughly to remove any dust, cobwebs, or loose debris. A clean surface will ensure better adhesion for your foam panels. Make sure the walls are completely dry before you start. If you plan on adding a wood frame later or need to locate studs for any reason, mark their locations on the floor or ceiling now.
Step-by-Step Installation: How to Install Used Foam Board in Your Basement
With your planning and preparation complete, you’re ready to start transforming your basement. This section will guide you through how to install used foam board effectively.
The first step is measuring and cutting your reclaimed foam panels. Measure the height and width of the wall sections you’ll be insulating. Transfer these measurements to your foam panels. For accurate cuts, use your straight edge or T-square as a guide. Thinner boards (around an inch or less) can often be cut using the “score and snap” method: make a deep score with your utility knife along your line, then gently snap the board. For thicker boards, a hand saw (like a drywall saw) or a specialized foam cutter will provide cleaner results. Take your time when cutting around obstructions like pipes, electrical boxes, or windows to ensure a snug fit.
Once your panels are cut, it’s time for applying adhesive and attaching the panels to your concrete or block walls. There are various foam board adhesives available; ensure yours is compatible with polystyrene. A common application pattern is an “S” bead across the back of the panel, or a continuous bead around the perimeter with a couple of “X” or cross beads in the middle. Follow the adhesive manufacturer’s instructions for the recommended amount and pattern. Press each panel firmly onto the wall, ensuring good contact. Aim for tight butt joints between adjacent panels to minimize gaps. If you’re applying multiple layers of foam for a higher R-value, stagger the seams between layers like you would with bricks.
An optional method is to install the foam between framing members. If you plan to build a wood stud wall in front of your concrete wall (perhaps for easier drywall attachment or running wiring), you can install the foam after the frame is up. In this case, you would cut the foam panels to fit snugly between the studs, securing them with adhesive or relying on a friction fit if the studs are spaced appropriately.
After all the main foam panels are in place, the next crucial step is sealing all seams and gaps. This air sealing is vital for the insulation to perform optimally. Use a compatible seam tape (like house wrap tape or a tape specifically designed for foam boards) to cover all the joints where foam panels meet. For any larger gaps, such as around the perimeter of the walls (where the foam meets the floor or ceiling joists) or around penetrations like pipes and wires, use expanding foam sealant. This will create a continuous air barrier, preventing drafts and improving energy efficiency. Taking care with these DIY reclaimed insulation best practices will pay off.
Finishing Touches & Important Considerations
With the foam installed and sealed, you’re on the home stretch. However, there are a few more important considerations and finishing touches to ensure your project is safe, compliant, and ready for whatever you have planned for your newly insulated space.
Depending on your local building codes and climate, you might need to install a vapor barrier. In some basement situations, particularly in very cold climates, a vapor barrier (typically a plastic sheeting like polyethylene) is installed on the warm-in-winter side of the insulation (meaning, on the interior, over the foam). Its purpose is to prevent moisture from your interior air from condensing within the wall assembly. However, many rigid foam insulations (especially XPS) are quite impermeable to moisture themselves, and an additional vapor barrier may not always be necessary or even recommended. Always refer to your local codes and, if unsure, consult with a local building professional.
One of the most critical points is the fire barrier requirement. Most building codes across the country mandate that rigid foam insulation, due to its combustible nature, must be covered by an approved thermal or fire barrier when installed on interior surfaces like basement walls. The most common fire barrier is 1/2-inch drywall. Other materials like 23/32-inch wood structural panels may also be acceptable in some jurisdictions. Do not skip this step; it is absolutely essential for safety. Emphasize checking and strictly complying with your local building codes on this matter.
If you envision a fully finished basement, you’ll likely want to proceed with framing and drywall. You can build a wood or metal stud wall directly in front of your newly installed foam insulation. This provides a convenient cavity for running electrical wiring and a solid surface for attaching drywall. Once the framing is up, you can hang and finish the drywall as you would in any other room.
Finally, don’t forget cleaning up. Gather any foam scraps. While XPS and EPS are not typically accepted in curbside recycling programs, check with your local waste management facility or Green Insulation about potential recycling or proper disposal options for larger offcuts.
The Benefits Realized: Enjoy Your Newly Insulated Basement
Congratulations! By installing reclaimed rigid foam insulation, you’ve made a significant improvement to your home. You can now look forward to a basement that is noticeably more comfortable year-round, with reduced energy bills as your heating and cooling systems don’t have to work as hard. You’ve also likely increased your home’s usable square footage and taken a positive step for the environment by choosing sustainable reclaimed XPS or EPS.
We hope this guide has empowered you to tackle your basement insulation project. Using quality reclaimed materials from Green Insulation not only saves you money but also contributes to a greener planet.
Further Resources
Ready to start your own DIY basement insulation project? Visit GreenInsulationGroup.com today to explore our current inventory of high-quality reclaimed XPS, EPS, and Polyiso rigid foam panels.
Have questions or need a quote for your project? Don’t hesitate to contact us! Our team is ready to help you find the perfect reclaimed insulation solution for your needs.
For more information on insulation and sustainable building, check out these other articles on our site: